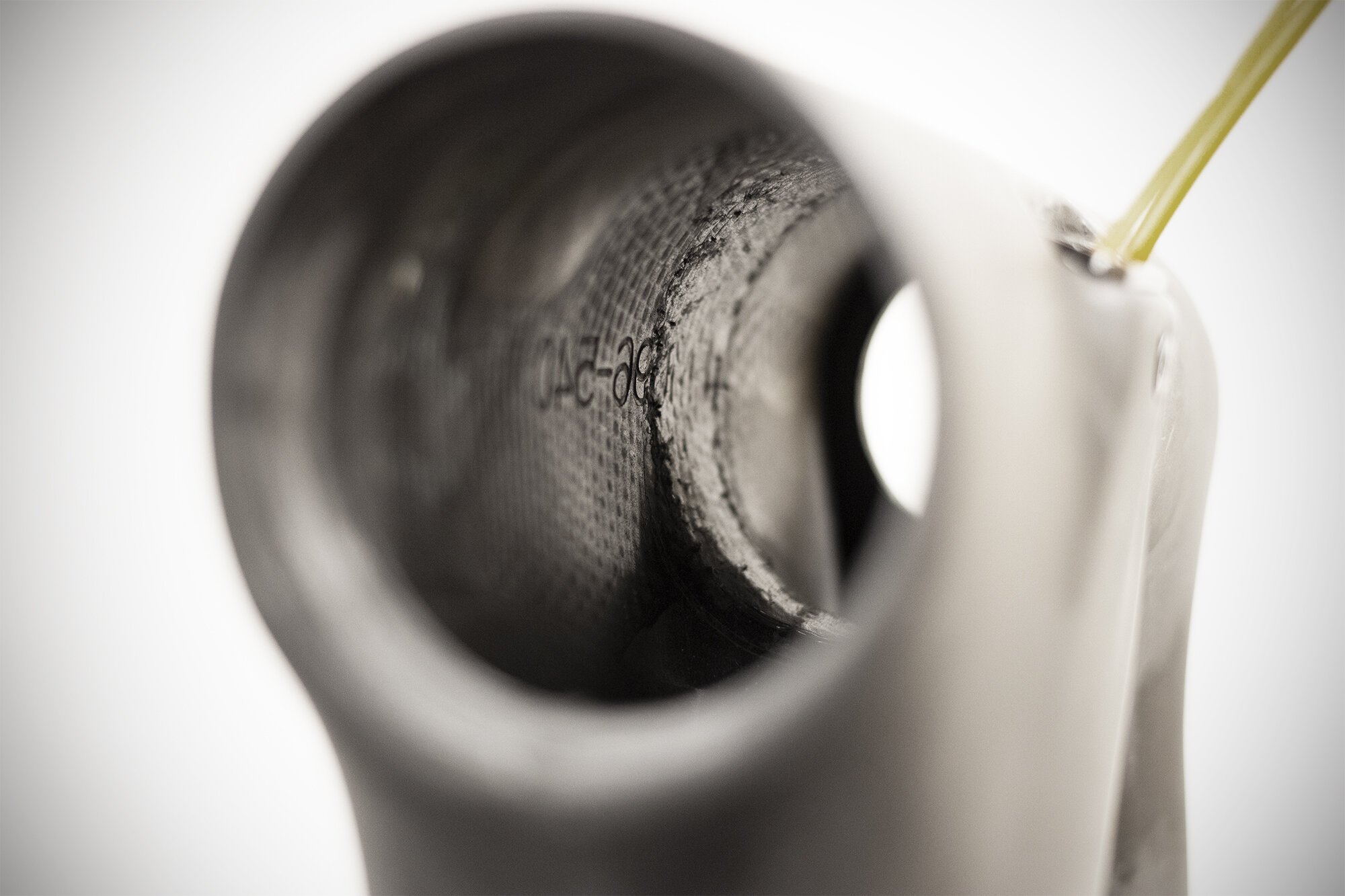
Our frames.
Forwards Carbon Fibre Frames.
We wanted to take a little time to tell you about our frames as it’s often one of the first questions we’re asked.
This page has been put together to explain all the buzz words and things that you will read on the website and all over the internet. Our frames are open mould and are made from UD, Toray carbon fibre. They are manufactured using the EPS moulding process and are tested to EN standards.
We’re just making a point about all that jargon as it will all be explained on this page. So, sit back with your preferred beverage and let’s get into it.
Open Mould.
What are open mould frames?
Our frames are known in the industry as open mould. They come from a reputable manufacturer in China whose business is to produce extremely high quality carbon fibre frames for companies such as us and certain models for larger bicycle manufacturers all over the world. Our frame manufacturer are specialists in carbon fibre and know the material extremely well, they are experts in bike frame design and they adhere to strict testing standards and working practices.
We can modify the design and specifications of the frames and forks which we purchase from our factory to suit our requirements and ultimately offer our customers the very best product to meet their needs. We buy our frames directly from the manufacturer and ship them directly to our build facility in the UK.
Using open mould frames is how many new bike brands start. This is due to the knowledge required to design a frame from scratch and the exceptionally high costs of making the moulds. It simply would not be possible to start this way without significant funding that would need to be passed onto the customer. This is where an experienced frame designer and manufacturing facility is essential.
The frames that we use are made from Toray carbon fibre which we’ll talk about next. Toray carbon fibre is made in various grades. The grades are used depending on the application we require. Our frames are manufactured using the EPS process and are tested in the factory to EN standards. Both of these are explained on this page also.
We offer a 2 years warranty against manufacturing defects on all of our frames and forks for absolute piece of mind. This obviously does not include crash damage or normal wear and tear.
We are currently looking into a heavily discounted crash replacement scheme to support our customers in the event of an accident.
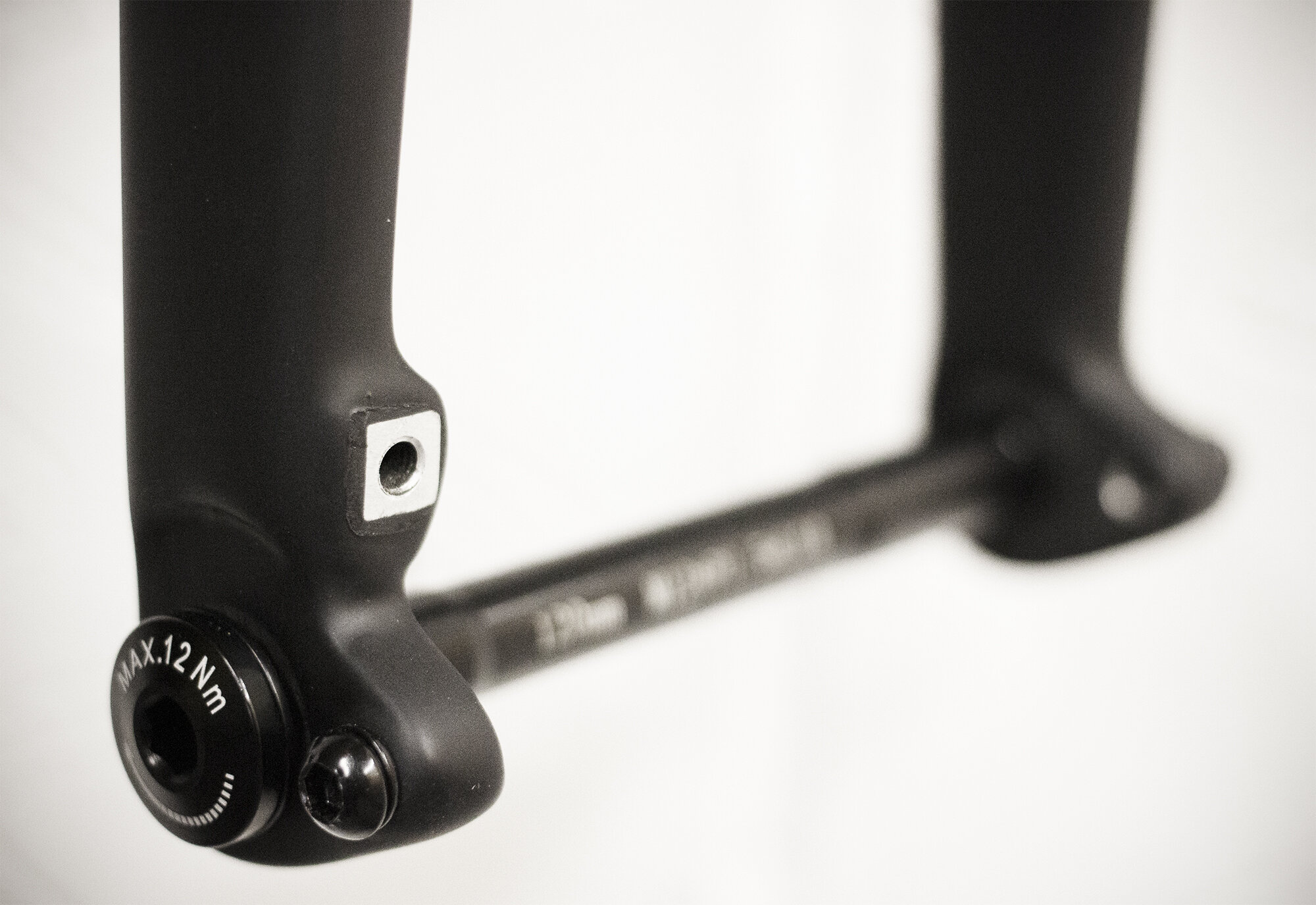
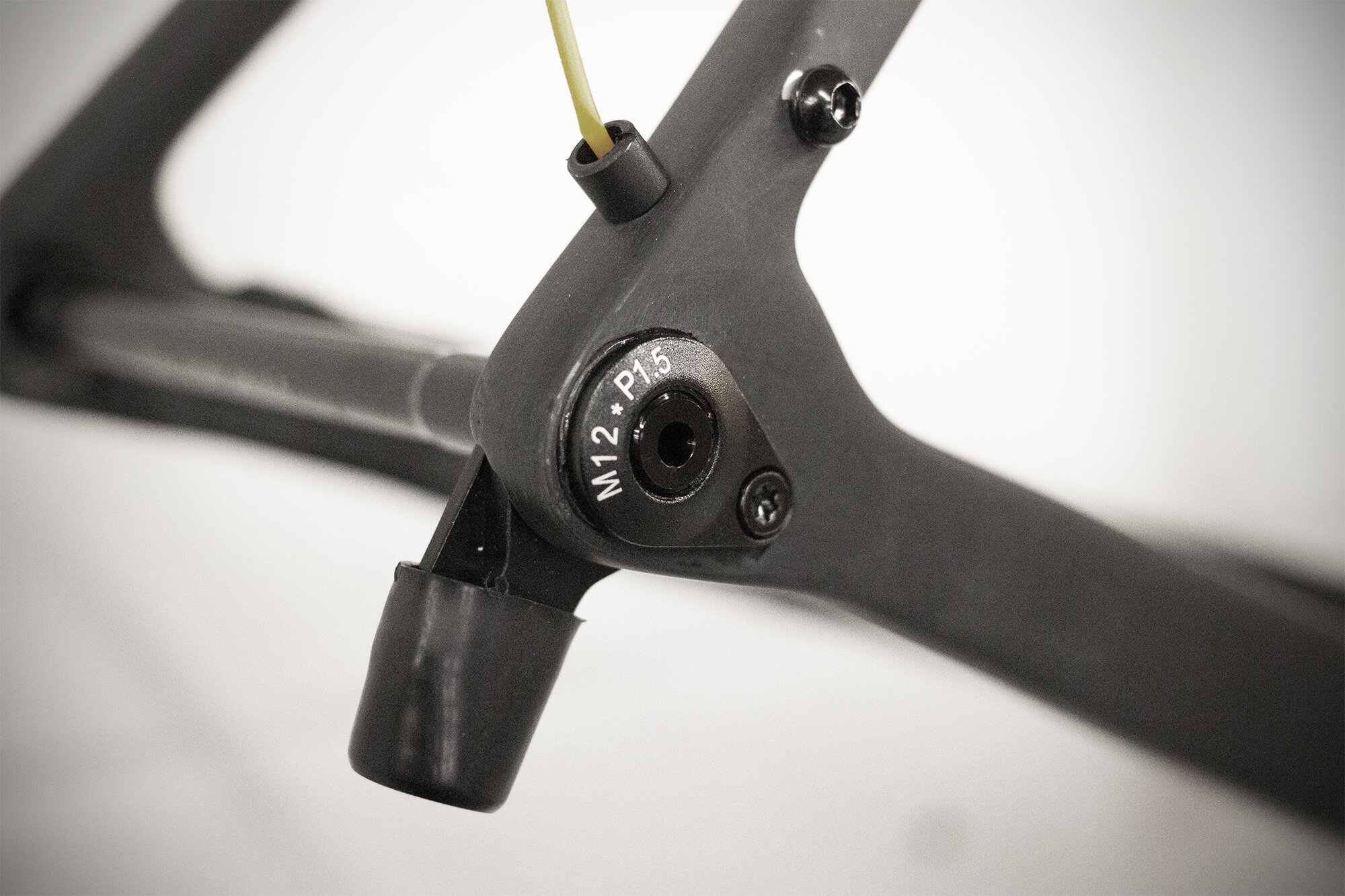
UD Carbon Fibre.
What is unidirectional carbon fibre?
Unidirectional (UD) carbon fibre is carbon fibre reinforcement with all the fibres aligned in the same direction. Unidirectional reinforcement makes it possible to create incredibly strong, light components by precisely orientating the carbon fibre to provide maximum strength in the direction where it is needed most.
Our frames use unidirectional carbon fibre for these reasons.
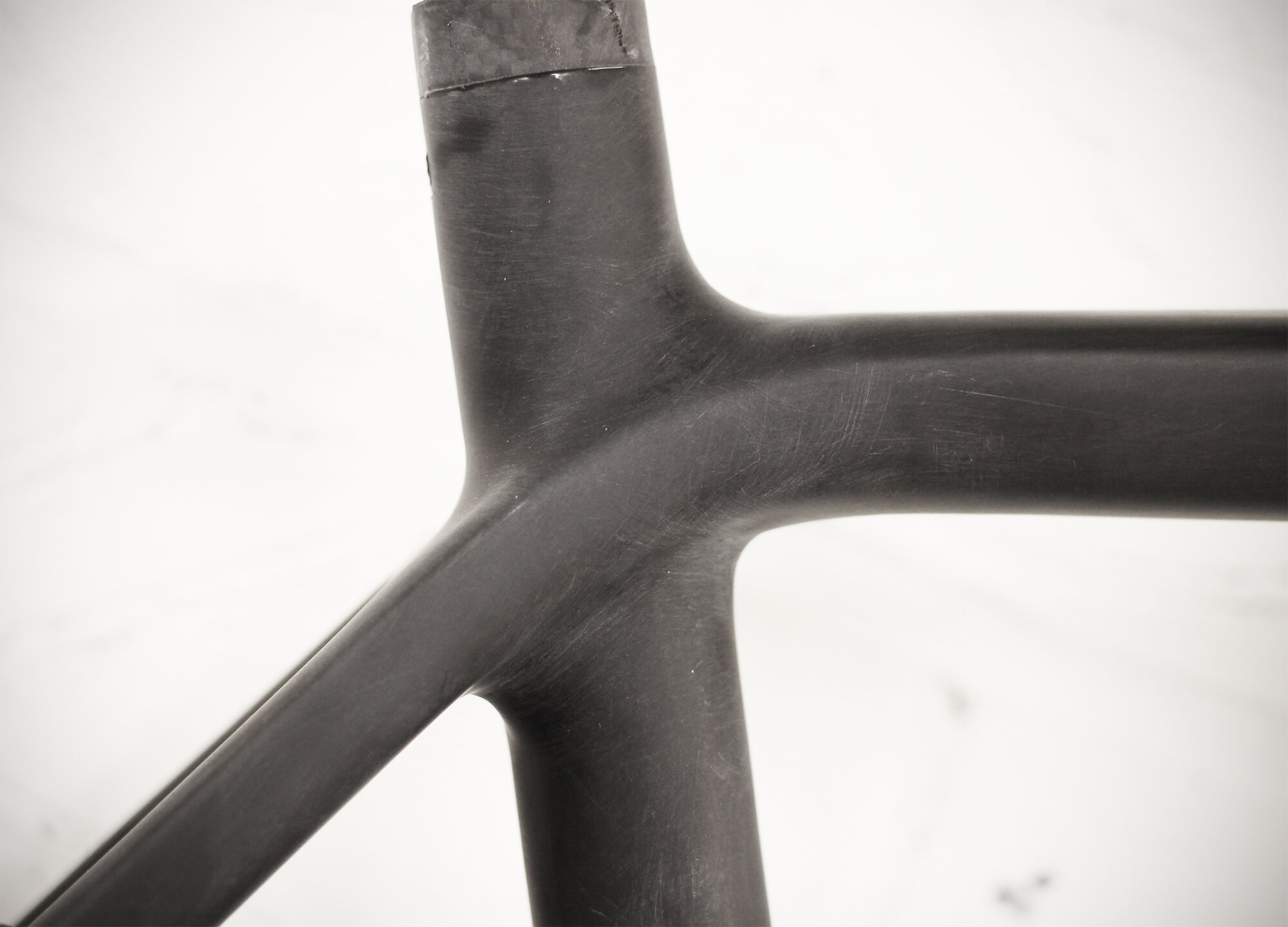
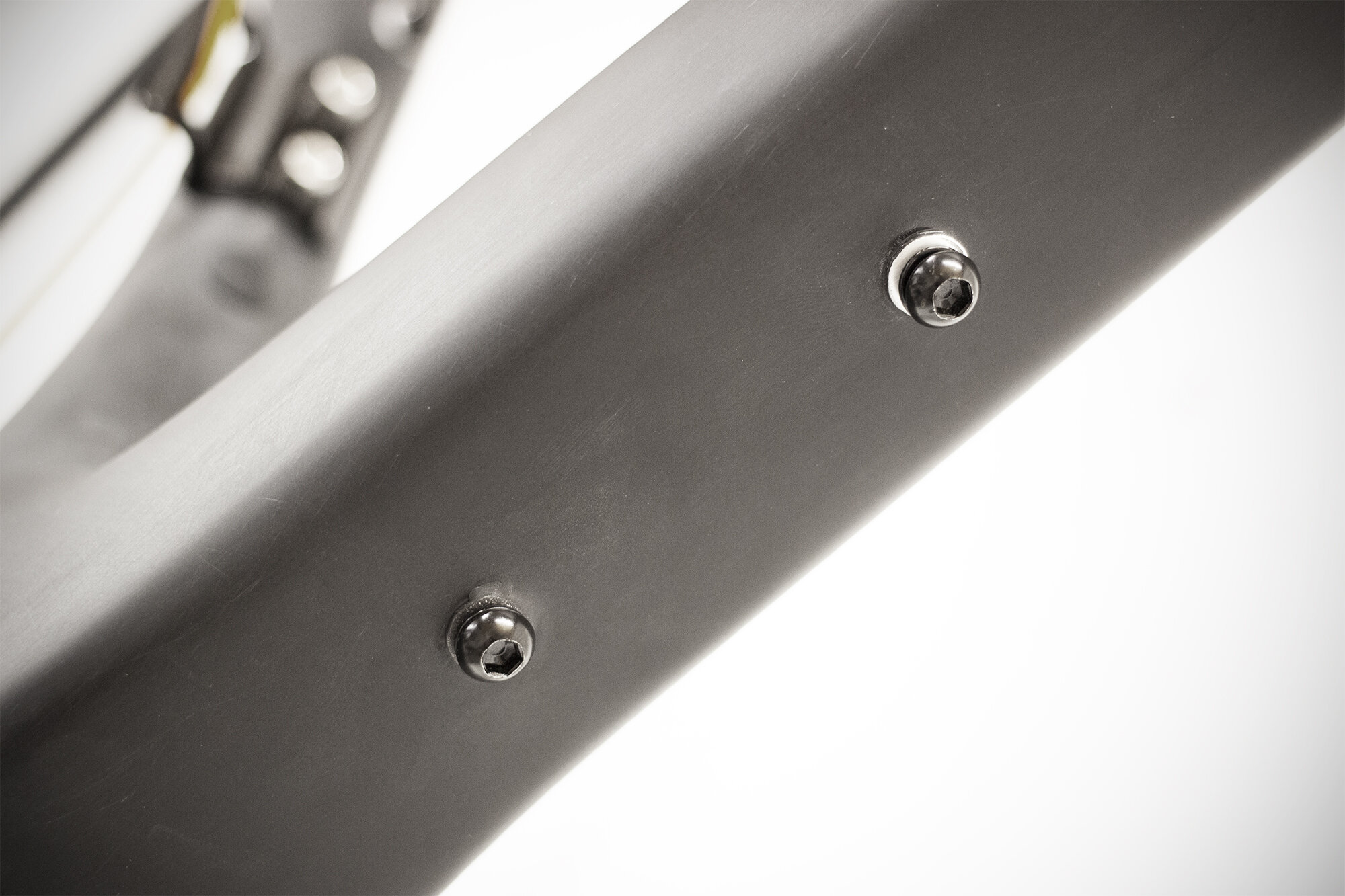
Toray Carbon Fibre.
What is Toray carbon fibre?
Toray is the world's largest manufacturer of carbon fibres and continues to work tirelessly on research and development. They produce carbon fibre for many sectors from sports and leisure applications to general industrial use. TORAYCA™ has been used in various ways thanks to its exceptional lightness, strength, and stiffness. Toray, the world leader, continues to grow in the field of advanced composite materials and is widely used for carbon fibre bicycle manufacturing.
Our frames are made from T700, T800, T1000 and the super light models are made from 60ton carbon fibre. Our frames also have a mix of carbon fibres in what is known as the lay up. Lay up is the name of the process where the carbon fibre sheet pieces are laid onto forms and into the moulds to make up the complex shapes that will eventually make up the finished frame or part. The layup and mix are essential in the frames design and this is all trusted to the vast experience of our chosen factory. Our gravel bike and mountain bike for example are a mix of T700 and T800. The multiple layers of carbon fibre create what is called a laminate.
The T in the carbon fibre grade stands for Toray which is the manufacturer and the following number is the grade. In general, the higher the number the lighter and stronger the carbon fibre. Grades are chosen for every application and placement in the frame design based on how the frame will be used in the end requirements of the location of the placement. Simply going all out on T1000 for example isn’t necessarily the best way as it may make the finished bike too harsh to ride for long periods of time and be more fragile in certain circumstances. It could also be more expensive than necessary for the chosen application.
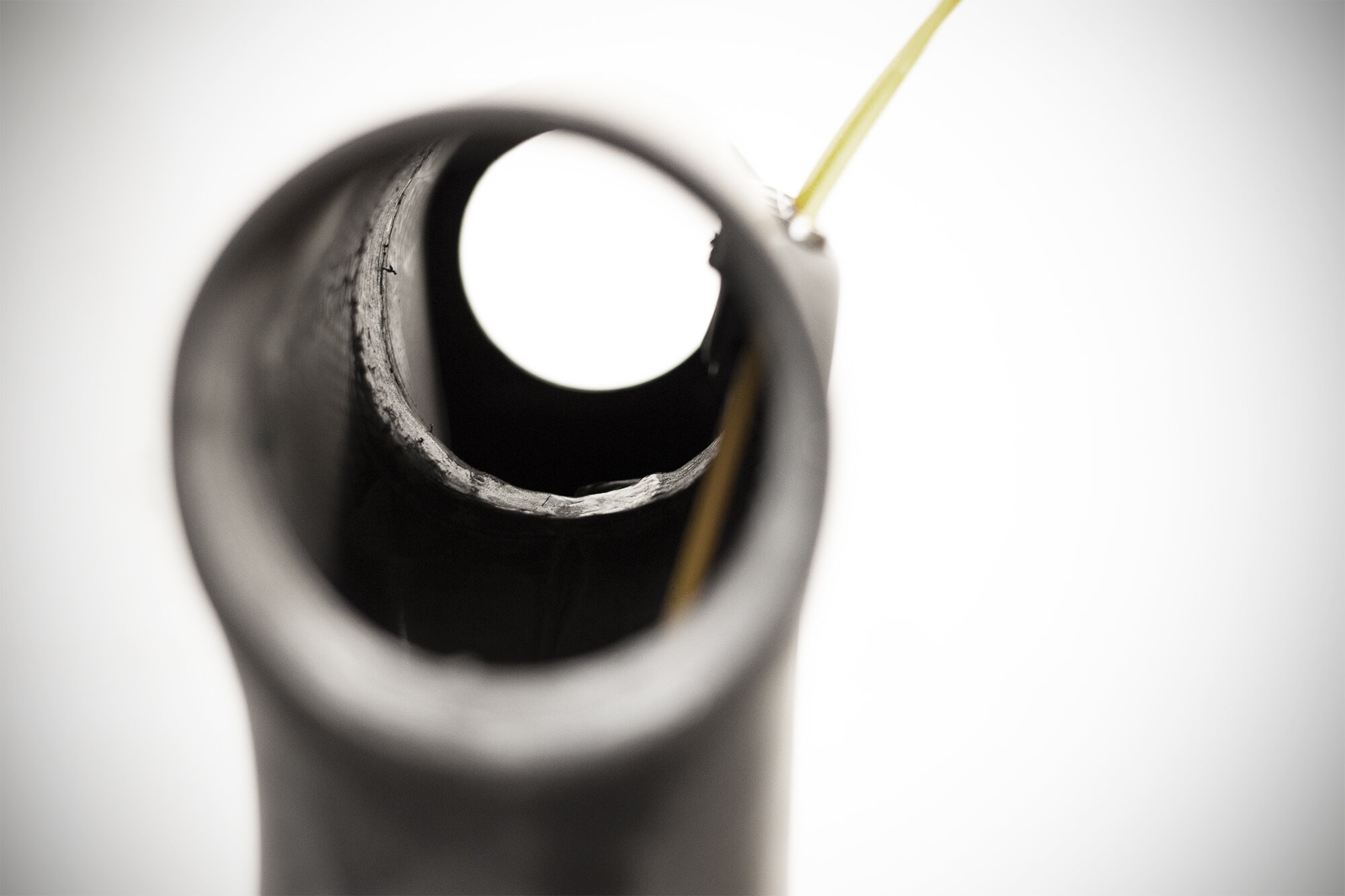
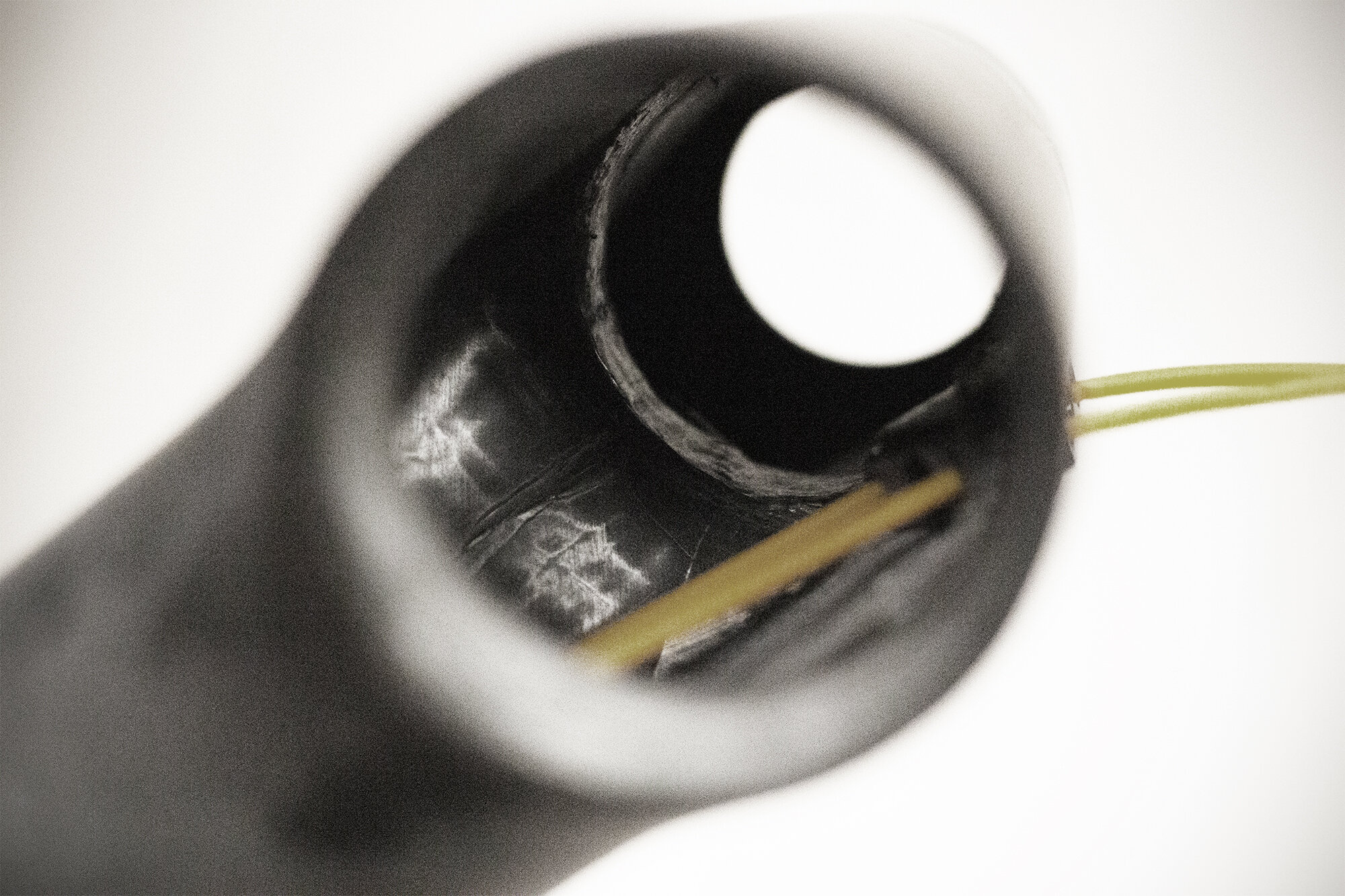
EPS Moulding.
What is EPS moulding?
EPS stands for Expandable Polystyrene System. EPS moulding is the standard for creating carbon frames, forks and other parts and is used for the very best carbon fibre bikes around the world.
The EPS process utilises a machined one-piece monocoque mould and a polystyrene form to create a carbon fibre bicycle frame. In terms of the complexity of manufacturing carbon fibre, it is relatively easy to make a frame look smooth and seamless on the outside, but what’s on the inside is equally as important. Making a carbon fibre frame involves compressing layers of carbon weave and epoxy resin into a mould to get the desired shape. Traditionally, before the EPS process, inflatable bladders were used inside the frame to force the material into the mould. Unfortunately, because of the restricted shape of a bladder it can’t be precisely controlled. Wrinkles or inconsistent thickness in the finished walls can sometimes be present. These irregularities can lead to de-lamination, voids or premature stress fractures as every fold and every wrinkle is a potential point of failure. By using the EPS, you get internal surfaces as smooth and wrinkle-free as the smooth exterior. This increases the strength due to the uniformity of the fibres with consistent wall thickness and no wrinkles. The result is a lighter, stiffer and more consistent final product.
The way the process works is that Polystyrene forms, known as EPS forms, are made to the shape that you want the various parts of the frame to be. Laminated carbon fibre is then wrapped around all of the individual parts and placed into a monocoque mould. When heated in an oven and air pressure is added, the individual beads in the EPS forms swell. If they were not within the mould they’d reach 40 times their original size. Constrained by the mould, this exerts pressure on the inside of the carbon fibre, pushing it exactly into the mould and the desired shape with consistent thickness and no wrinkles. Once cured, the frame is removed from the mould and the polystyrene form removed from inside. The inside is then left as smooth as the outside without the potential imperfections of the traditional bladder mould method.

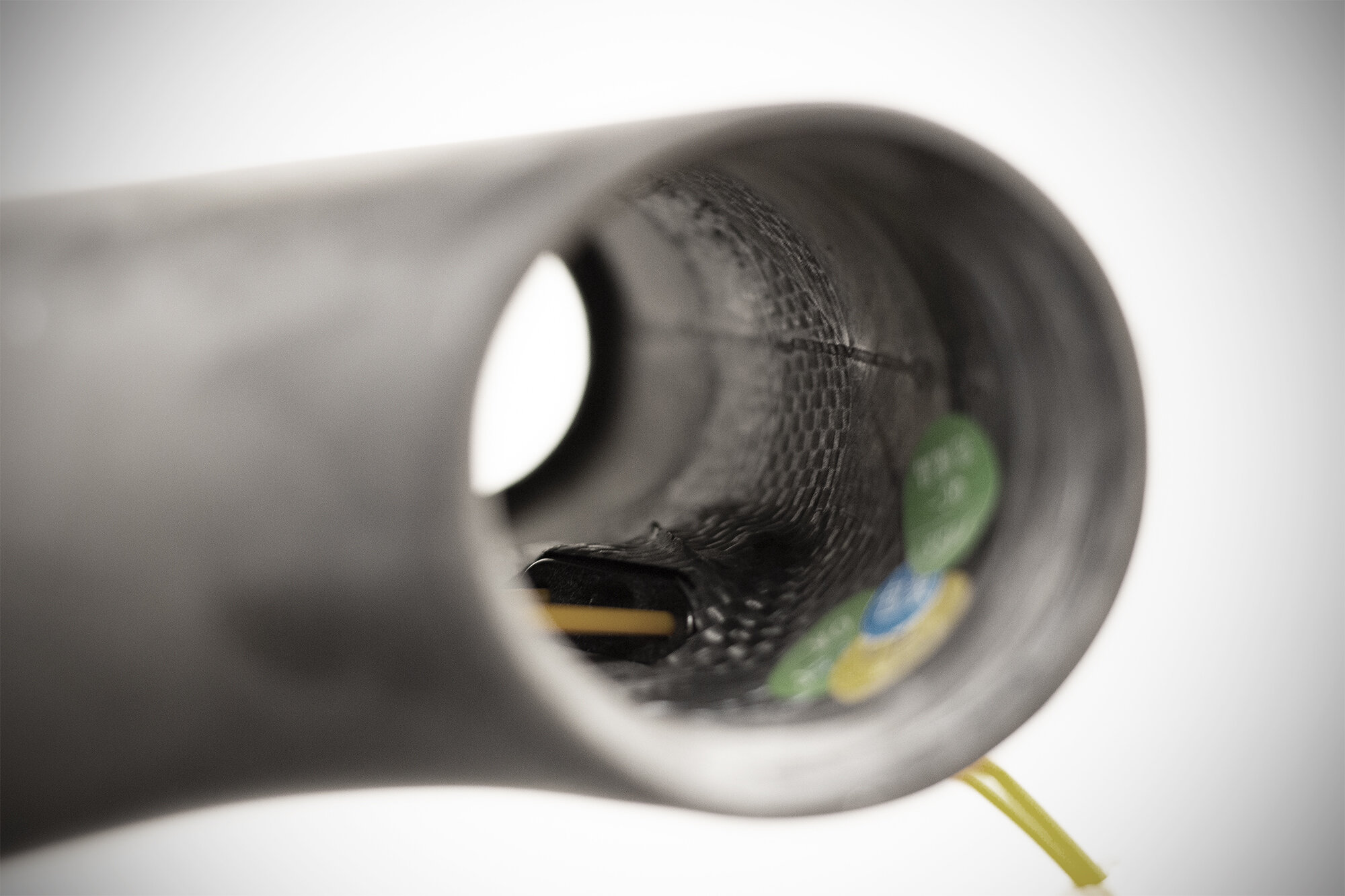
EN, European Standard.
What is the EN standard?
All of our frames are subject to EN standards. This testing is performed in house at our factory which is based in China.
An EN standard or European Standard is a document that sets out requirements for a specific item, material, component, system or service, or describes in detail a particular method or procedure. These standards facilitate international trade by ensuring compatibility and interoperability of components, products and services. They bring benefits to businesses and consumers in terms of reducing costs, enhancing performance and improving safety.
In terms of our frames, forks and parts, this ensures that they are safe to use and that all of the components fit and perform as they should. They are quality checked at each stage of the manufacturing process and labelled each time they pass a work station to confirm they have passed that phase.
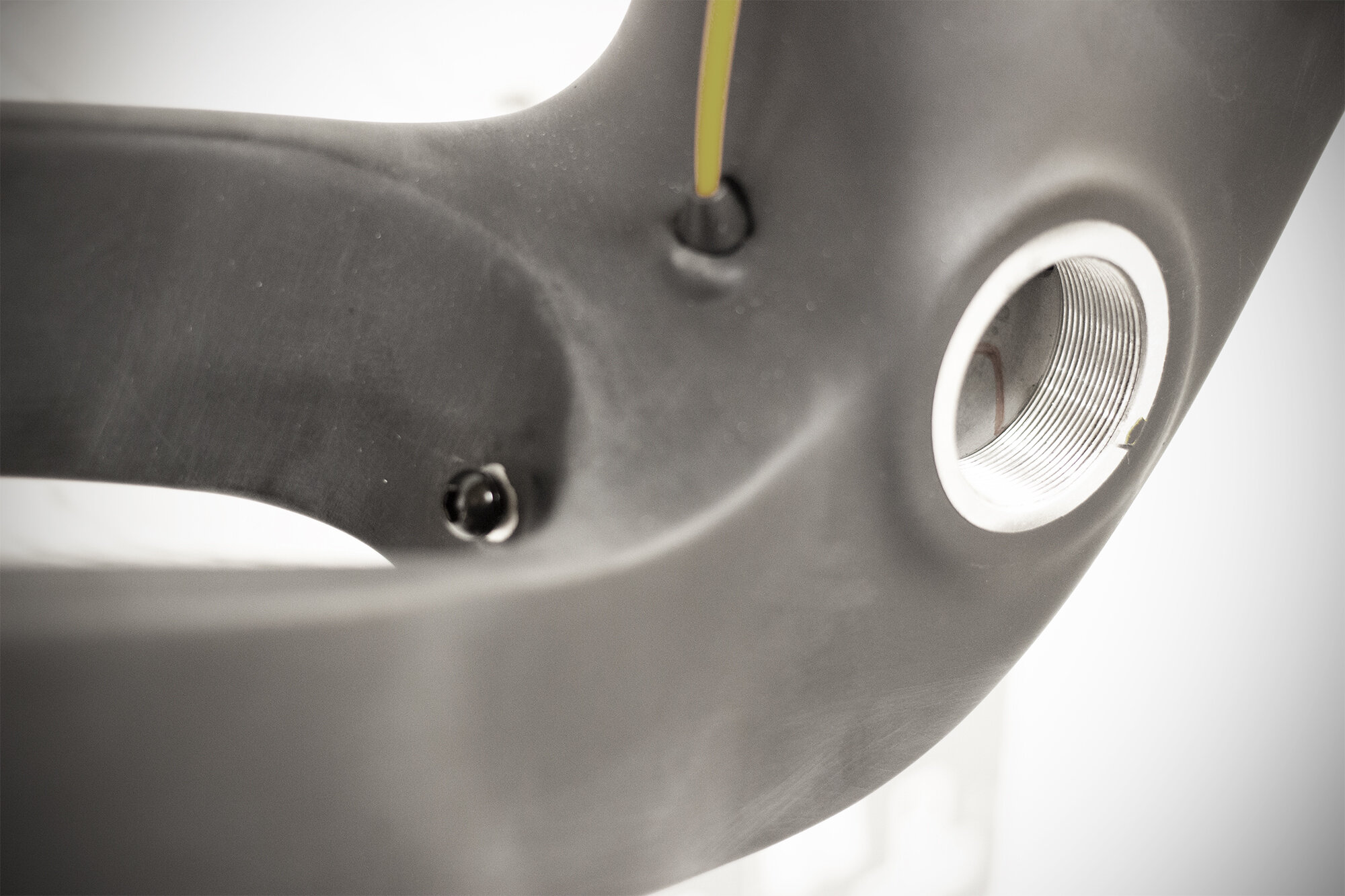
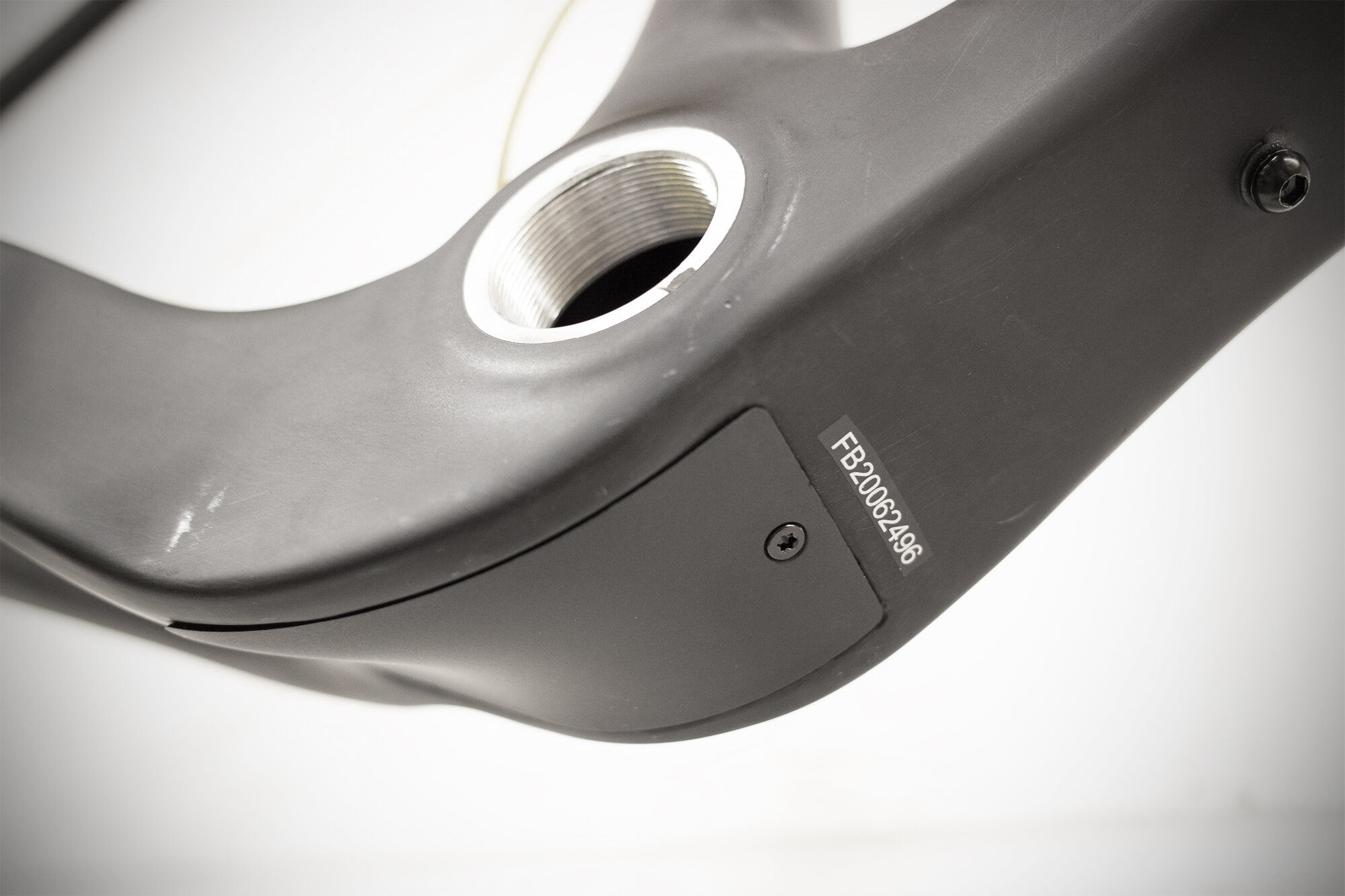